CONTACT US!

Electrical Testing of Rubber PPE:
USA Safety & Training is your
one-stop-shop for all of your Electrical
Testing, Arc Flash, and PPE needs in the
Electrical Industry with our
State-of-the-Are Testing Lab.
USA Safety & Training is proud
Distributor of all equipment and PPE
products in the Electrical Industry. If you
are looking for new inventory or simply
wanting to replace existing products we
have you covered. While testing these
products, we can replace any failed
equipment at our location.
USA Safety & Training facilitates Von Corp - In-House Automatic Testing of lineman’s Gloves, Sleeves, Blankets, and Line Jumper up to 50,000V AC, 100,000V DC or both. Allows Testing to ASTM D120, F496 and IEC 60903 Standards.
USA Safety & Training First lines of defense when it comes to preventing contact with energized electrical components and/or electrical power lines are rubber insulating gloves, commonly known as High Voltage Gloves. High Voltage Gloves must meet the requirements of the current ASTM D120 specifications and NFPA 70E standards. OSHA enforces these requirements as a part of their CFR 1910.137 regulation. These standards dictate manufacturing criteria as well as testing and retesting requirements for Lineman Gloves. OSHA requires the use of rubber insulated gloves for those persons working on or near energized circuits and/or other electrical sources that are considered either high or low-voltage applications.
CONTACT US TODAY!
-
Best in the business Customer Service!
-
Quick Turnaround!
-
Computerized and Documented Testing Results!
-
Storage, Cleaning, and Handling!
-
NEW Inventory to replace existing products!
-
Automatic retesting notifications and emails to customers!
USA Safety & Training Testing Process:
-
Wash (by washing machine or hand) and dry Gloves, Blankets, Sleeves, Hoses, and Jumpers
-
Visually inspect rubber PPE and thoroughly checking for defects, recording all visual failures accordingly.
-
Electrically test rubber PPE with no visual failures using the voltage/time necessary based on the standard, and pulling all PPE with failures from the machine to record as failed while testing the remaining PPE again.
-
Dry, date stamp and prepare all the PPE that passed for shipment back to you while auto e-mailing or faxing notification of test completion with a copy of the test report and failed merchandise.
-
Ship back all rubber PPE to you with a test report, or simply pick-up PPE at our testing lab facility.
Classifications:
Employees who work in close proximity to live electrical current may require a variety of electrically insulating protective equipment. The Occupational Safety and Health Administration (OSHA) outlines this in its electrical protective equipment standard 29 Code of Federal Regulations (CFR) 1910.137, which provides the design requirements and in-service care and use requirements for electrical insulating gloves and sleeves as well as insulating blankets, matting, covers and line hoses.
Electrical safety gloves are categorized by the level of voltage protection they provide and whether or not they’re resistant to ozone.
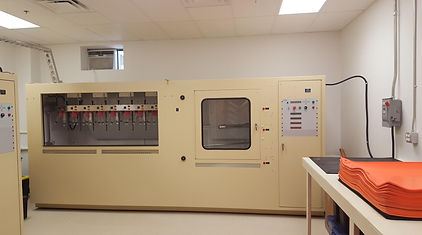
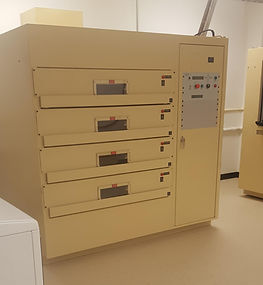
Inspection:
Once the electrical safety gloves have been issued, OSHA requires that “protective equipment be maintained in a safe, reliable condition.” This requires that the gloves be inspected for any damage before each day’s use. Gloves must also be inspected immediately following any incident that may have caused damage. OSHA also requires that insulating gloves be given an air test along with the inspection.
The air testing method is described in ASTM F496-14a Standard Specification for in-Service Care of Insulating Gloves and Sleeves. The glove is filled with air, either manually or with a powered inflator, and then checked for leakage. The leakage is detected by listening for escaping air or by holding the glove against the tester’s cheek to feel air releasing. In accordance with ASTM F496-14a, gloves and sleeves should be expanded no more than 1.5 times their normal size for Type I, and 1.25 times normal for Type II during the air test. The procedure should then be repeated with the glove turned inside out.
Since sleeves cannot be inflated, they should be inspected along the edge as they are rolled. Rolling will stretch the sleeve along the edge, making cuts, tears and ozone cutting more visible. After the outside of the sleeve is inspected, the procedure should also be repeated with the sleeve turned inside out.
Before each use, gloves and sleeves should be inspected for holes; rips or tears; ozone, cutting or ultraviolet damage; and signs of chemical deterioration per ASTM F1236-14, Standard Guide for Visual Inspection of Electrical Protective Rubber Products. Gloves and sleeves should also be examined to determine if they show any damage as a result of chemical contamination, particularly from petroleum products. The first sign of chemical exposure is swelling in the area of contamination. Should any glove or sleeve be exposed to chemical contaminants or suspected of any other physical damage, they should be retested per ASTM D120-14a requirements.
Testing:
In addition to the daily inspection, OSHA requires electrical safety equipment to be subjected to periodic electrical tests as specified in 29 CFR 1910.137(c)(2)(viii). Rubber insulating gloves must be tested before first issue and every six months thereafter; upon indication that the insulating value is suspect; after repair; and after use without protectors. If the insulating gloves have been electrically tested but not issued for service, they may not be placed into service unless they have been electrically tested within the previous 12 months.
Storage:
To help ensure the integrity of the gloves and worker safety, gloves need to be stored properly when not in use. Manufacturers suggest lineman gloves be stored out of direct sunlight, in a cool and dry location away from sources of ozone. They should be stored in a glove bag (one pair per bag) and then hung-up versus being laid down on a flat surface. Rubber insulated gloves should never be folded in the storage bag. Creasing insulated gloves may cause cracking which could shorten the useful life of the gloves.
We Service:
Glove Testing- capable of testing In-house electrical glove testing helps you meet ASTM F496 requirements, tests electrical rubber gloves from Class 00 to Class 4, 10.5" to 18" lengths and all cuff styles. Clothespin style holders are provided which do not pinch the gloves or sleeves. The center spacing is 9 inches to accommodate 50K.V. gloves.
Sleeve Testing- Capable of testing all standard sleeves in accordance with the latest ASTM D1051 and F496 standards. Sleeves are tested using the clothespin method and 2” diameter spacers are used to eliminate sharp bends in the sleeves.
Blanket Testing- capable of testing 5 blankets. All standard size and voltage blankets including Class IV 22x22 and 36” x 36” solid or splits can be tested.
Line Hose and Hood Testing- Capable of testing two six foot long line hoses.
Line Jumper Testing- One or two line jumpers may be dielectrically tested in the test tank in place of gloves or sleeves.
​
And More........